What are the common types of cold room compressors
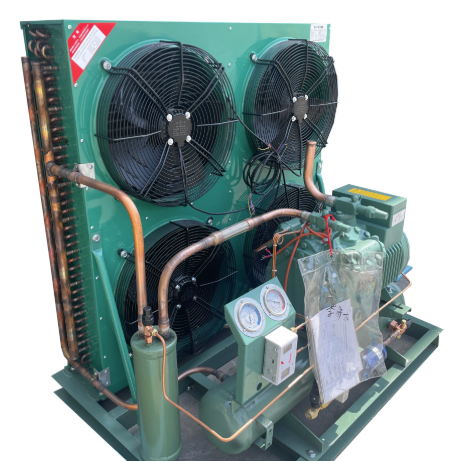
The cold room compressors are the core part of the operation of the refrigerator. It is because of the compressor that the entire cold storage can maintain a suitable operating temperature to ensure the normal storage of food and other products in the cold storage. However, there are many types of cold room compressors, and we need to configure compressors according to different cold storage conditions. As an expert in cold storage overall solutions, SDpanel will introduce you to more compressor information.
Cold room compressors used in industrial applications come in many shapes and sizes. The following are the types of compressors commonly used in cold room refrigeration systems, their main characteristics and typical applications.
Reciprocating Compressors
The earliest type of compressor is the reciprocating compressor, which compresses the refrigerant using a piston driven by a crankshaft in a cylinder, and controls the refrigerant flow through the inlet and exhaust valves.
Advantages of reciprocating compressors
Reciprocating Compressors have relatively low initial cost, mature technology, simple design, are suitable for small capacity applications, have good efficiency under various operating conditions, and are available in semi-hermetic and fully-hermetic types.
Disadvantages of reciprocating compressors
Reciprocating compressors have higher noise and vibration levels, more moving parts (potentially higher wear and maintenance costs), and less efficient capacity control, and are generally not suitable for high-volume applications.
Application of reciprocating compressors
Reciprocating compressors are mainly used in small and medium sized cold rooms. (e.g. walk-in coolers/freezers in restaurants, small warehouses, florists, butchers).
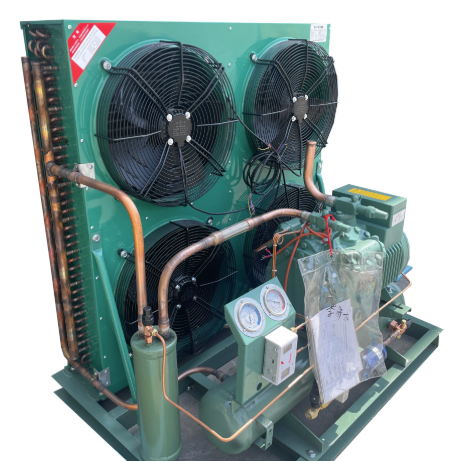
Screw Compressors
Screw compressors have replaced reciprocating compressors. A simple rotating screw is sufficient to ensure smooth system operation. It is less likely to wear out and is easier to lubricate than reciprocating compressors. It employs two meshing screw rotors, which are located inside a cylinder. As the rotors rotate, the refrigerant gas is trapped in the cavity between the rotors and its volume decreases along the length of the rotors towards the exhaust port, where it is compressed.
Advantages of screw compressors
Screw compressors have high capacity and efficiency (especially at full load), excellent capacity control, are rugged and reliable in continuous operation, have less vibration than reciprocating compressors, and are suitable for large systems.
Disadvantages of screw compressors
Screw compressors have the highest initial cost, require a more complex oil management system, may have higher maintenance costs, are larger in size, and if not perfectly controlled, efficiency at part load may drop significantly.
Application of screw compressors
Large refrigerated warehouses, distribution centers, industrial food processing facilities, and large supermarket central systems. The mainstay of large refrigeration systems.
Centrifugal Compressors
Centrifugal compressors are equipped with rotating vanes and employ two interlocking helical scroll discs to form a compression chamber that moves toward the center, thereby reducing volume and increasing pressure. On the other hand, centrifugal compressors are almost always used in industrial environments. These compressors are one of the most common types.
Advantages of centrifugal compressors
Centrifugal compressors are quiet, efficient, low vibration, good resistance to liquid shock, stable capacity control and compact size.
Disadvantages of centrifugal compressors
Centrifugal compressors have higher initial costs than reciprocating compressors, may have limited capacity compared to large screw units, and are usually fixed displacement.
Application of centrifugal compressors
Increasingly used in a number of small, medium and even large cold rooms (medium-sized warehouses, distribution centers, large restaurant storage rooms). Extremely common in modern modular condensing units due to high efficiency and reliability. It is suitable for cold storage in low and medium temperature environment.
In the current market, piston compressors are being replaced by centrifugal compressors, which are increasingly being used in small and medium-sized cold rooms due to their excellent efficiency, reliability and quietness. Screw compressors, on the other hand, are firmly established in the market for larger equipment. Cold room compressor selection depends heavily on the specific size of the cold room, temperature requirements, budget, and noise sensitivity. If you have similar questions you can consult the refrigeration engineers at SDpanel.