How to choose right clean room panels for clean room
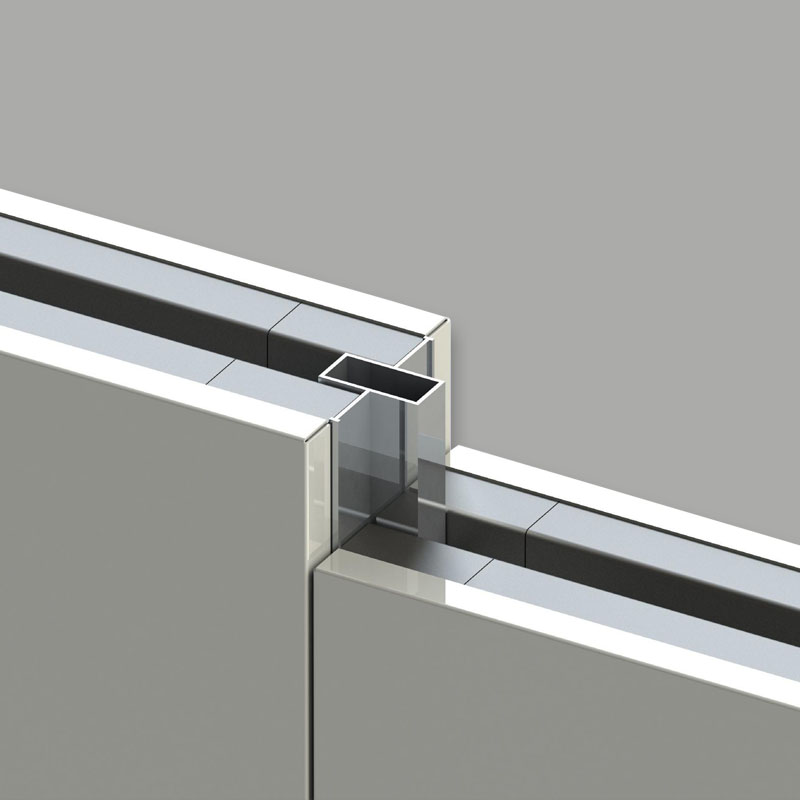
In the cleanroom construction of pharmaceutical, semiconductor, food, daily chemical and other industries, choosing the right clean room panels are crucial to the success of the project, which affects cleanliness, compliance, durability and long-term cost.
Clean room panels come in a variety of specifications, including panel thickness, surface material, core material, and installation method. Although certain parameters are specified in the design drawings to determine the specifications of the cleanroom, they do not necessarily determine a single solution. SDpanel has a set of clean room solutions and will help customers choose the best solution based on the actual situation of the project.
Prioritizing clean room panel configuration
Clean room panels meets structural requirements
For the choice of clean room panels, first of all, to ensure the safety of the structure, in order to consider the clean room panels for the functional requirements of the clean room.
Selection of clean room panels that comply with fire safety
Clean room panels include clean room ceiling panels, clean room partition panels and clean room wall panels as well as Clean room roof panels, so there are mandatory standards for the fire resistance and fire rating of each component in order to comply with local building codes. The most common requirements are related to fire performance and fire resistance. The most common requirements relate to fire performance and fire resistance ratings. Fire resistance affects the choice of core material for clean room panels, and rock wool clean room panels and Glass magnesium panels are commonly used for most clean room panels. On the other hand, the fire resistance rating is largely dependent on the thickness and core composition of the panels, and SDpanel cleanroom panels are available with different combinations of cores and thicknesses, with fire resistance ratings of up to 3 hours.
Selecting clean room panels that meet load-bearing requirements
For the cleanroom load-bearing requirements, cleanroom roof panels and cleanroom wall panels are required to be calculated, general design drawings will have clear requirements, usually use 0.5 mm galvanized steel can meet, and the thickness of the cleanroom plate is not only with the fire-resistant requirements, but also with the load-bearing of the cleanroom, especially the cleanroom roof panels, of course, general design of the cleanroom will take into account the above issues; and under normal circumstances. Cleanroom wall panels will generally be 3-5 meters high and will not be deformed due to self-weight. For extra-long panels, increasing the thickness of the edge keel material, adding reinforcement or adding core material are common methods to increase the load-bearing capacity of the panels. For Clean room Partition panels, which are mainly used for enclosure, the conventional specification can be used, while Clean room Ceiling panels need to be calculated because they may need to carry more loads.
Selecting clean room panels that meet the function of the cleanroom
Cleanrooms in different industries have different functional requirements and different grades, which should be noted when selecting clean room panels
Clean room grades
If the only requirement is a cleanroom rating, then ordinary cleanroom sheets are usually sufficient. Of course the requirements for cleanrooms vary from class to class, with ISO 5 (Class 100) and lower requiring cleanroom panels with ultra-tight seals, smooth surfaces and minimal seams. For example, in the Class-B area of a pharmaceutical cleanroom that has a long-term demand for VHP disinfection, the paint surface of conventional cleanroom panels cannot meet the requirements. conventional cleanroom panels cannot meet the requirements. The aerospace industry and the semiconductor industry have their own specialized characteristics and requirements.
Clean room panels meet industry requirements
In the pharmaceutical, biological laboratories and corrosive environment industry, the requirements of corrosion resistance and easy to clean, and the skin is not easy to fall off, so the general selection of stainless steel clean room panels; the electronics industry and general industry, may be with the consideration of affordable cleanroom panels, the general selection of galvanized steel to do the skin of the cleanroom panels; for the aseptic requirements of the industry, such as hospitals, will choose the antimicrobial coating of the clean room panels.
Suitable range of various types of clean room panels
EPS Clean room panel
EPS Clean room panel is best suited for ISO 7/8+ class cleanrooms and is ideal for cost-sensitive projects due to the low price of EPS Clean Sheet. However, due to the flammability of the EPS material, avoid using it in high temperature (>75°C), fire hazardous areas.
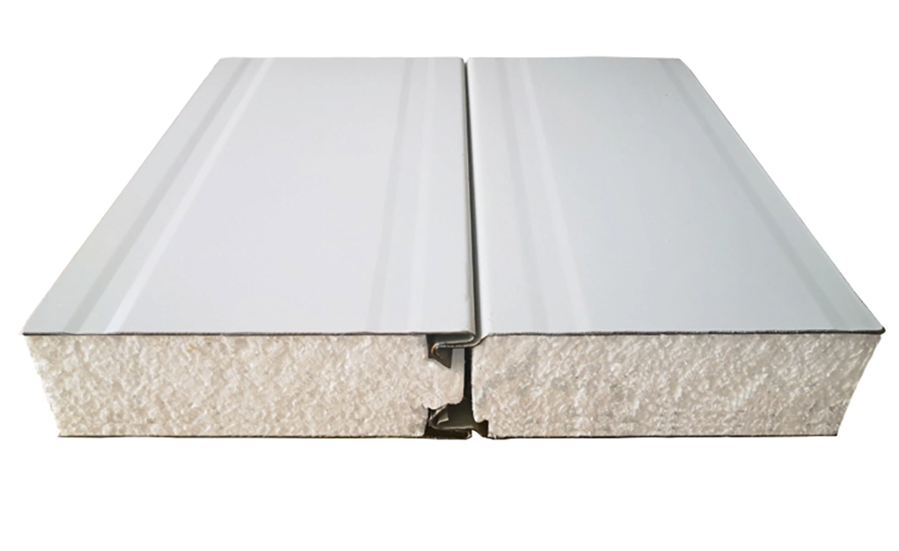
Rock Wool clean room panel
Rock Wool clean room panel is more fire-resistant, suitable for projects with firewalls, soundproofing, high-temperature areas, and higher requirements for fire protection. It has the disadvantage of heavier self-weight, certain requirements on the structure, and higher cost.
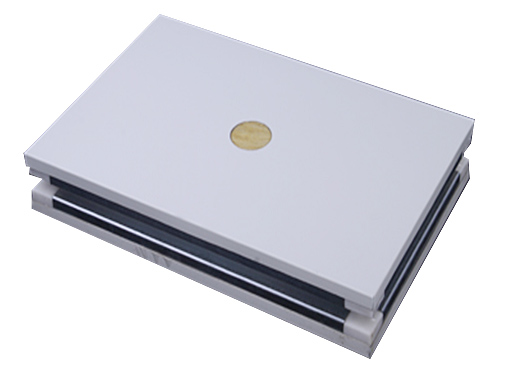
PIR/PU clean room panel
PIR/PU clean room panel is best suited for areas suited for ISO 5/6 class cleanrooms , highly insulated (lowest K-value), and moisture resistant. For some projects check the fire certification of the product and eliminate the inclusion of graphite costs.
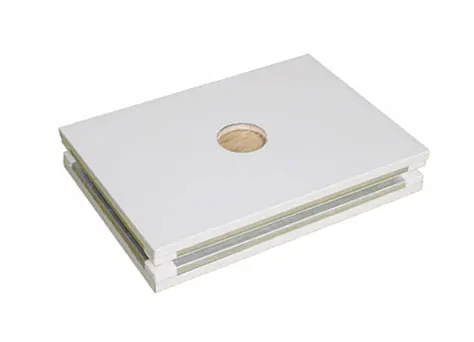
Honeycomb Aluminum Panel
Honeycomb Aluminum Panel has a moisture resistant core, which makes these panels highly resistant to corrosion. Also, these panels are effective against mold and fungus growth in enclosed spaces, making them most suitable for cleanrooms that require a sterile environment. Due to their high structural strength and light weight, they are often used as ceilings in some cleanrooms. However, the high cost is the main factor restricting their use.
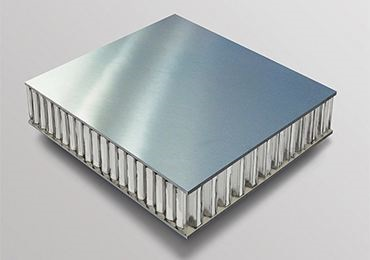
Cleanroom engineering is a complex system engineering project. Choosing the most suitable clean room panels product requires comprehensive consideration of various factors of the cleanroom enclosure structure. As a Chinese brand in the cleanroom panel industry, SDpanel has accumulated rich experience in many cleanroom engineering implementation projects and has a strong technical team. They continue to research and apply innovative materials, improve product production processes, and optimize product structure design to meet the differentiated needs of cleanrooms in different industries.