Production process of PU sandwich panel
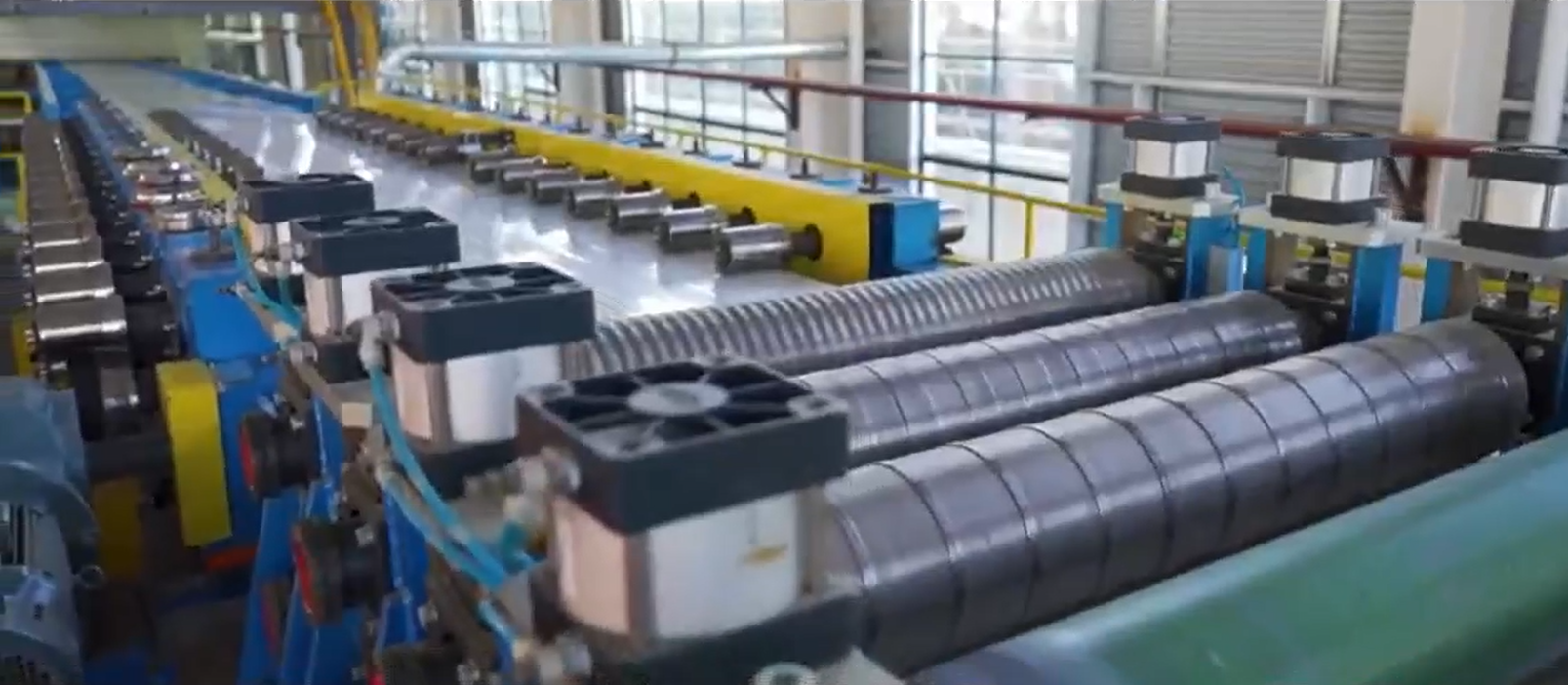
PU sandwich panel is increasingly used in construction and refrigeration due to their good thermal insulation properties. The quality of PU sandwich panel is particularly critical in applications. To understand the quality of the product, you need to truly understand the production process of the product. The production process of PU sandwich panel is as follows:
Including unwinding, profile forming, mixing and foaming, curing, shearing, cooling, automatic palletizing and packaging process.
Material preparation of PU sandwich panel
Material preparation is mainly panel preparation. First, the pre-coated/galvanized steel coil or aluminum coil is loaded onto the decoilers, then the pre-coated/galvanized steel coil or aluminum coil is cleaned and pre-treated, and the panel is brushed and chemically pre-treated (such as chromate or chrome-free treatment) to ensure optimal adhesion and corrosion resistance. Then the panel is formed, and the panel passes through a series of forming rollers to form the required profile (trapezoidal, micro-ribbed, hidden fixing) to enhance rigidity, drainage and interlocking. The upper and lower panels are formed separately.
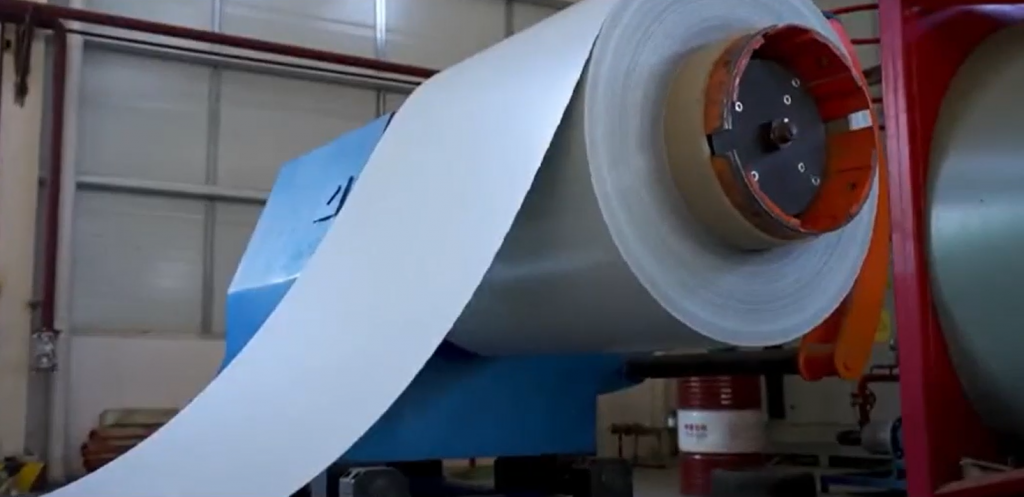
Mixing and Foaming of PU sandwich panel
Mixing and foaming is the core part of PU sandwich panel production. The polyurethane foam is then prepared by mixing the polyol and isocyanate in the correct proportions, usually in a mixing head. It then enters the gap between two continuously moving, highly polished steel bands, which are sprayed with adhesive. As the foam reaction proceeds, the liquid expands rapidly, filling the cavity between the veneers. An adhesive layer is typically used to affix the sheet metal to both sides of the foam core. At this point, any other layer, such as a vapor barrier or insulation, may be added.
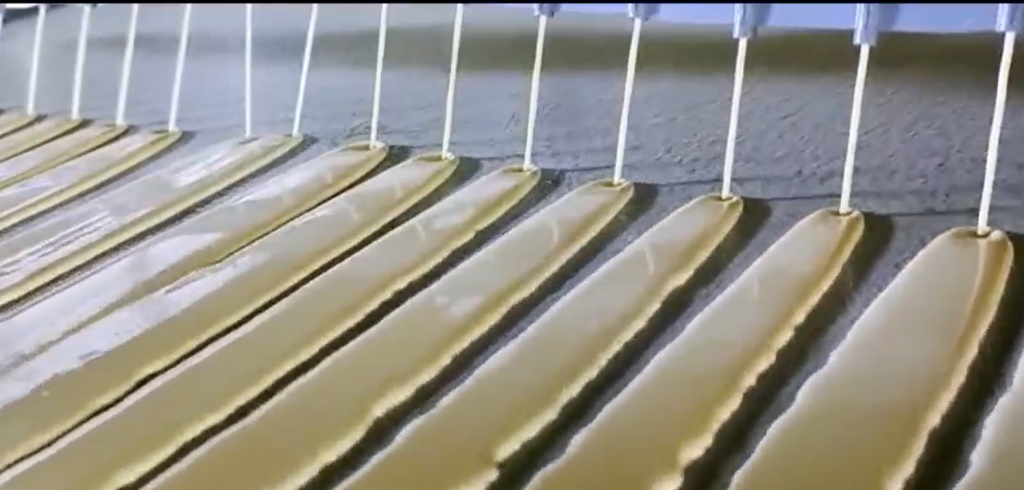
Curing and shearing of PU sandwich panel
The laminator section is a long, heated tunnel (20-60 meters). Temperature zoning is precisely controlled to control exothermic reactions and optimize curing. The gap between the upper and lower conveyor belts determines the final sheet thickness. Side chains/seals are used to contain the expanding foam. After the sandwich panels are placed in the laminator, they are heated at the appropriate temperature to cure and harden the foam. After leaving the laminator, the panels are sent to a cooling conveyor. Ambient or forced air cooling allows for complete curing and thermal/dimensional stabilization of the foam.
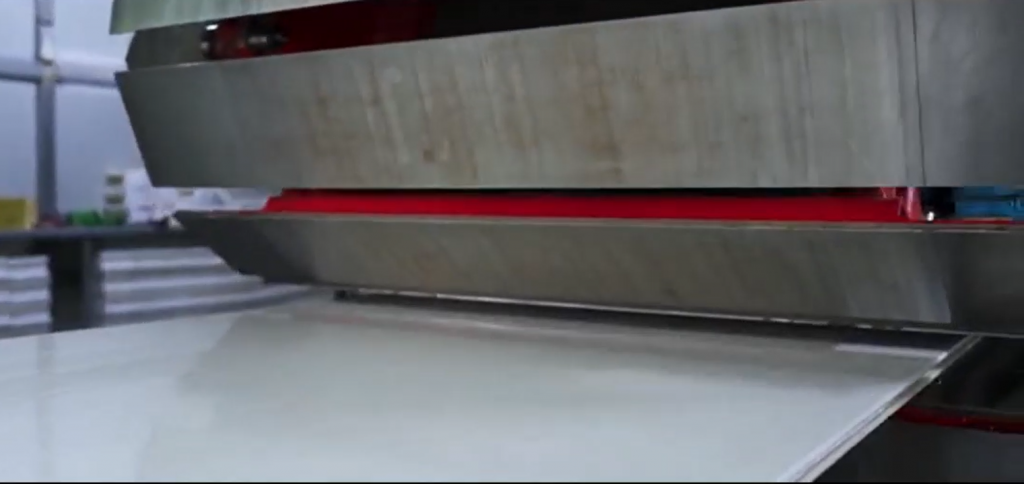
Automatic palletizing and Packaging
Before palletizing and packaging, the PU sandwich panels are first cut into the sizes and shapes required by the customers using tell-fly saws. Then, an automatic stacker lifts the panels onto pallets or A-frames. Protective film/paper is applied on top, bundled and packed for transportation.
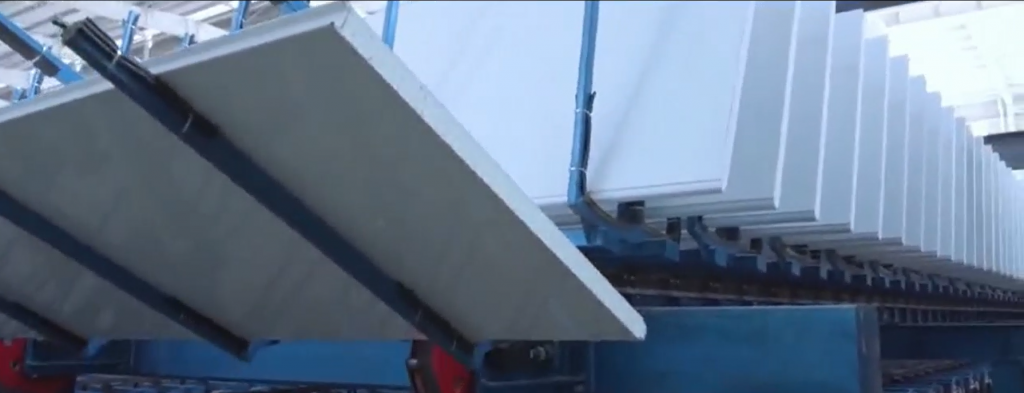
This is a simple description of the PU sandwich panel production process. SDpanel has a high-speed full polyurethane production line imported from Germany, with an annual production capacity of 1 million square meters. If you want to learn more about the polyurethane formula, production flow, and various properties of PU sandwich panels, please let me know!