What is an ISO 5 cleanroom
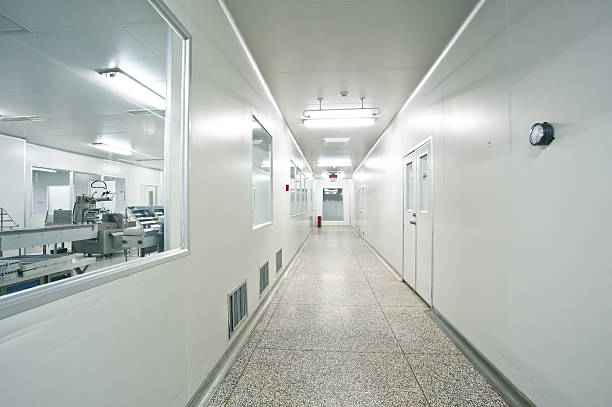
An ISO 5 cleanroom (classified under ISO 14644-1) is a controlled environment where the concentration of airborne particles is tightly limited to ≤ 3,520 particles per cubic meter (0.1 particles per cubic foot) of size ≥0.5 µm. With stricter cleanliness standards than ISO 6, ISO 5 cleanroom is widely used in industries such as semiconductor fabrication, sterile pharmaceutical production, nanotechnology, and advanced medical device manufacturing.
An ISO-5 cleanroom classification corresponds to FED 209E class 100 cleanroom classification. The FED 209E cleanroom rating system is a US-based British rating system, which has been historically used in United States for industrial cleanrooms such as semiconductor cleanrooms and printed circuit board cleanrooms. his stringent level of air cleanliness ensures optimal working conditions for industries that require an ultra-clean environment.
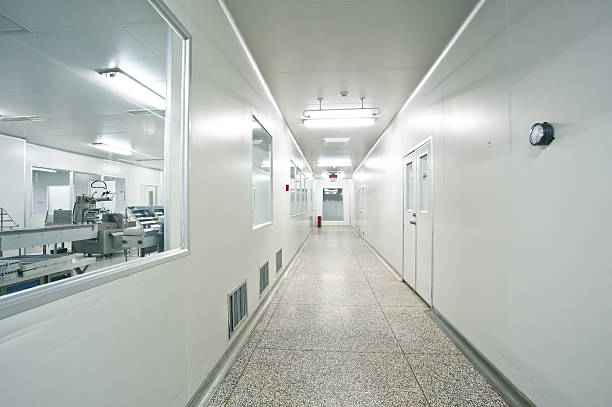
Here’s a detailed breakdown of ISO 5 cleanroom:
Key Specifications:
Parameter | Requirement |
Particle Limits | ≤ 3,520 particles/m³ (≥0.5 µm) • ≤ 832 particles/m³ (≥1 µm) • ≤ 29 particles/m³ (≥5 µm) |
Airflow | Unidirectional (laminar flow) at 0.45 ±0.1 m/s (90 ±20 ft/min) |
Air Changes | 240–600+ per hour (depending on room size/occupancy) |
Filtration | HEPA filters (99.99% efficiency at 0.3 µm) or ULPA (99.999% at 0.12 µm) |
Pressure Differential | Minimum +10–15 Pa vs. adjacent less-clean areas to prevent contamination ingress |
Critical Design of ISO 5 cleanroom
Materials & Surfaces
ISO5 cleanroom clean room panels, clean room ceilings and clean room partition panels should use smooth, non-shedding and anti-static materials such as stainless steel, seamless floors and epoxy coating surfaces; electronic/pharmaceutical industry clean room floors should use anti-static floors; equipment must adopt a smooth, seamless design to minimize particle accumulation and facilitate cleaning and disinfection.
Air Filtration design
Equipped with Ultra-Low Penetration Air (ULPA) filters or High-Efficiency Particulate Air (HEPA) filters to remove microscopic particles and contaminants. Air exchange rate typically ranges from 240 to 600 air changes per hour, ensuring a highly controlled environment.
Air flower Design
Primarily uses unidirectional (laminar) airflow, where air moves in a parallel flow pattern across the clean zone to minimize particle accumulation. Ceiling-mounted filters supply clean air, which is then exhausted through floor-level or low-positioned vents for efficient air circulation. The return air vents should be located close to the floor to capture outflowing particles.
Temperature & humidity design
Typically maintains temperatures between 18-22’℃(64-72°F)Humidity levels are controlled between 30-50% to ensure equipment stability and process reliability.
Applications of ISO 5 cleanroom
Pharma/Biotech: Sterile filling of injectables, vaccine production, cell therapy labs.
Medical Devices: Implant manufacturing, surgical kit assembly.
Electronics: Semiconductor wafer fabrication, nanotechnology R&D.
Healthcare: Hospital compounding (e.g., IV drugs), tissue culture labs.
Aerospace: Precision optics, satellite component assembly.
An ISO 5 cleanroom is essential for processes where microscopic contaminants can compromise product sterility, performance, or safety. Success hinges on integrated design (airflow/filtration), rigorous protocols, and continuous monitoring. If you need to know about the design and materials of ISO 5 cleanroom, please contact SDpanel designer